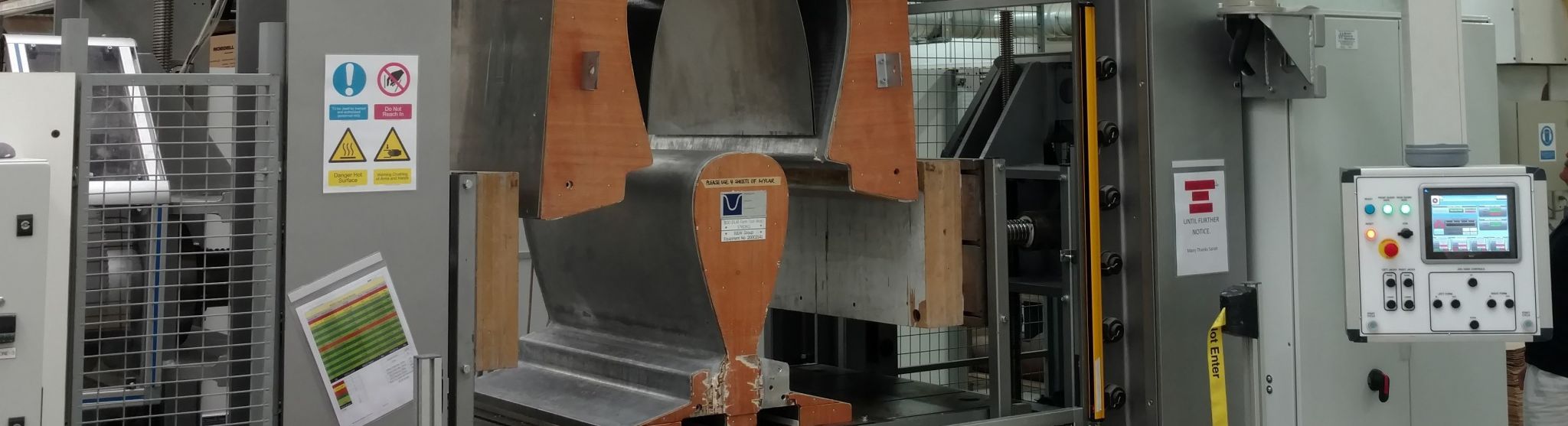
Forming press machines are key pieces of equipment in the production of highly precise metal components. From more traditional forming presses with simple yet effective functions, to customised specialty forming tools, this machinery is a crucial part of manufacturing processes.
Engineering metal components is necessary for a range of industries, which require accurate parts of all sizes to construct their final products. At Cambridge Dynamics, we have expert knowledge of just how versatile forming presses can be, promising consistency and quality every time.
All you need to know about forming press
The history of metal forming has its roots in blacksmithing, though this was updated with the advances of steam-powered machinery during the industrial revolution of the 1700s – 1800s. In the modern day, such processes have been updated again with computer numerical control (CNC) technology.
You might wonder: are stamp presses and forming presses the same? This is a common question, as people often use ‘pressing’ and ‘stamping’ interchangeably. While a stamping press is technically a type of forming press, it specifically involves shaping a piece of metal by stamping it between dies. ‘Forming’ is an umbrella term for many types of metal pressing, with slightly different machines.
Different press machines can be classified in various ways, such as by their powering mechanism (e.g. hydraulic), their function (e.g. stamping), or their driving structure (e.g. screw press). As a general term and process, forming is the shaping of material (primarily metal) via the application of pressure. However, the methods and machinery can vary for specific subsets of forming presses.
WHAT DOES A FORMING PRESS DO?
There are many metal forming operations that offer cost-effective manufacturing processes through the use of a high-tonnage press machine. A forming press can be configured with an array of tools to form the finished parts, whether the shape is simple or requires a combination of operations.
Here’s a quick overview of some of the different metal forming processes and how the components are shaped:
- Bending – folding along a single axis to form a specific angle (e.g. L or V shape)
- Blanking – punching out a flat shape to produce a 2D piece for further processing
- Coining – high-pressure stamping to compress the metal into a patterned shape
- Deep-drawing – stretching the metal out to a depth that exceeds its diameter
- Embossing – pressing shallow depressions into the metal to form raised/recessed designs
- Flanging – folding along a curved edge and creating a flange or flare
- Hemming – folding an edge back and up to make the edge stronger
- Punching – shearing slugs of metal out of the part that can then be recycled
- Rolling – passing metal through rollers to bend or flatten it
- Stamping – pressing sheet metal between a punch and die to stamp out a shape
- Turning – spinning a tube or disc of metal and cutting parts away as it rotates
There are many more possible pressing functions, but these are some of the most common processes. Each of these types may require different machinery, powered either mechanically (flywheel), hydraulically (pressurised fluid), mechanical servo (fast motors), or CNC automation.
HOW DO CNC FORMING PRESS MACHINES WORK?
CNC forming uses computer numerical control technology to automate bending, stamping, punching, or any other press machine function. Computer software can translate a model of your component into numerical code, which then directs the machine and its tools to create the shape. Sizes and angles are accurately measured down to fractions of a millimetre for fast precision.
Like non-CNC forming presses, a CNC machine will have a turret that drives down towards the bed, where the metal stock is placed. There can be custom shearing or stamping tools, or the use of a punch and die, to form components with multiple bends or cut-outs without having to manually re-adjust the machine. This speeds up the process considerably and reduces production costs.
When a combination of forming processes is necessary to create the component design, CNC machining is often the most practical choice. However, as this can be more expensive than other types of machining, it may only be worth the investment for larger production runs with a shorter lead time. Non-CNC forming machines can be cost-effective for smaller runs or production trials.
WHAT ARE THE BENEFITS OF FORMING PRESSES?
Forming presses have many benefits, which is why you’ll find them in use in a variety of industries. From home appliances to cars, cutlery to personal electronics, we all use products containing parts made by forming presses every day. Here are some of the advantages of forming press machines:
- Able to maintain precise standards repeatedly across large amounts of parts
- Suitable for short or long production runs, including small pilot runs
- Can combine multiple tooling techniques to streamline operations
- Reduces or eliminates the need for post-processing (e.g. cleaning)
- Often less expensive than other metal fabrication processes
- Can use different types and thicknesses of metal in the same press
- Manufactures components for diverse products across many sectors
Depending on the particular properties needed for the purposes of the product, you can choose from a range of metals and alloys. This often includes materials like stainless steel, aluminium, copper, brass, beryllium, and bronze. These can be in sheets, wires, cylinders, or other shapes. The best forming press solution will create the shape and volume within budget and time constraints.
FORMING PRESS SOLUTIONS FROM CAMBRIDGE DYNAMICS
With many years of experience producing parts across a range of industries and metal forming machinery, Cambridge Dynamics can provide the ideal solution to meet your manufacturing needs. No matter how challenging, we can complete a selection of forming applications, and help you to decide the most appropriate method for your component shape, materials, budget, and lead times.
If you’re interested in how Cambridge Dynamics can help you, get in touch with our team of experts today to discuss your metal forming needs. Fill out our online contact form or send an e-mail to enquiries@cambridgedynamics.co.uk, and we’ll respond as soon as possible. Alternatively, you can give us a phone call on 01480 459555 to speak to someone at our headquarters in Cambridgeshire.
FAQ’s
What are forming presses?
A forming press is simply a pressing machine that shapes a workpiece by applying pressure to it. Many companies have utilised forming technology and machinery to create their desired outcomes, as the appliance of pressure allows for a material to be shaped in many different ways.
Having been utilised for hundreds of years, forming presses are nothing new. However, through advancements in technology and mechanical expertise, these machines have been adapted and improved to create the excellent solutions we see today.
Here at Cambridge Dynamics we are happy to offer the very best in forming press machines, so each and every one of our customers can benefit from this way of creating their ideal product. Be sure to take a look at all that we have on site or get in touch with our team of experts if you’d like to receive an answer for your specific enquiry.
What are Forming Presses used for?
A forming press is a very useful device if you’re looking to produce the same shape on a large scale. This is why they are usually found in factories that need to produce the same product many times over.
As years have gone by, they have become a lot more powerful, efficient, and effective, meaning that in the modern day, these a forming press machine can work quicker and smarter than ever before.
They are versatile applications due to their ability to morph all kinds of materials in many different ways. For example, if you’re looking to stretch or bend a metal for the purpose of the exact item you’re trying to create, forming presses can do so.
Due to the robust, hard wearing materials that a forming press is made from, this kind of effect can be achieved easily, so this part of the process can be completed quickly.
If you’re looking for a machine that is fit for purpose and gives you the ability to work with speed and precision, one of our excellent forming press machine solutions could be exactly what you need.
How does a forming press machine work?
Put simply, press forming creates a desired shape out of sheet metal by deforming it under pressure. The metal stock is placed on the machine bed, then a ram is driven down and presses the metal to bend it into the required form. The more intricate the design of the part is, the more advanced the tooling technique needs to be. For example, CNC machining guarantees precision at faster speeds.
Various metal forming presses include the aforementioned stamping presses, which use dies to form the piece, and punch presses, which cut the shape by punching it out of the sheet. There are many forming techniques that these press machines can carry out, which we’ll discuss in further detail below. They can require standard tooling for basic shapes or custom tooling for complex shapes.
Forming presses are widely used to replicate the same shape over and over, producing large batches of this component relatively quickly. In its most straightforward form, such a pressing machine will create the piece from sheet metal with one stroke or press. For more complicated multi-dimensional pieces, the metal can be in a coil or tube, and requires several strokes in a multi-stage operation.