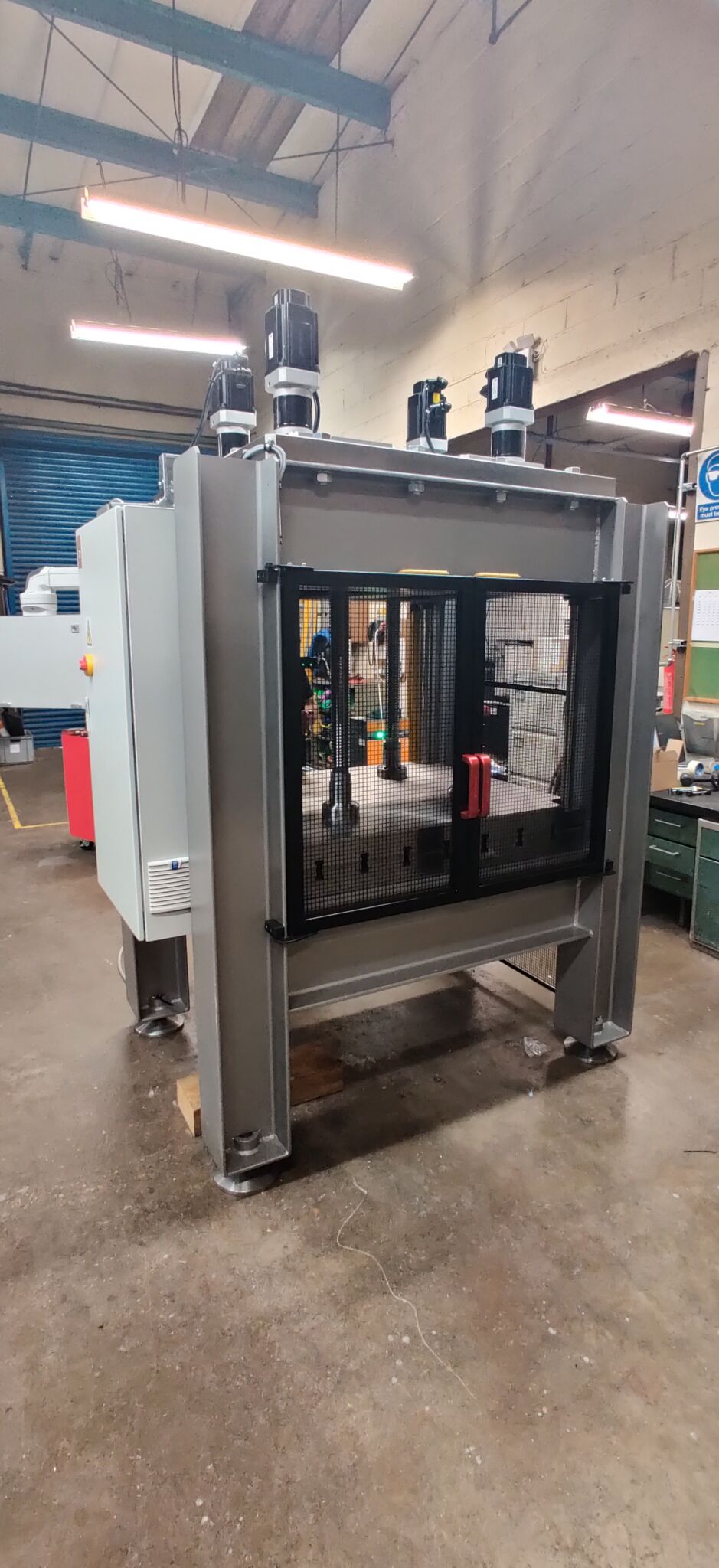
While composites are an invaluable resource within the manufacturing industry, they require sophisticated tooling and fabrication methods to shape them.
At Cambridge Dynamics, we specialise in the manufacture of a wide range of composite presses that are compatible with various composite and laminated materials.
Here, we’ll explain a little more about our manufacturing processes and how we work with composite presses that mould and form to an extremely high level of precision.
Composite Materials
Composite presses are used to provide the force and position control that is required to shape pieces of composite material during manufacture.
By “composite material”, we refer to a combination of two materials whereby the resulting composite exhibits improved properties, be it strength, durability, rigidity, longevity or even affordability.
Our presses work with many different composite materials, including fiber reinforced plastics or polymers – such as fiberglass or carbon fiber – wood composites like ply, and metal matrixes. Whatever the composite with which you intend to work, it’s highly likely that we will be able to supply a solution for you.
Cambridge Dynamics’ Composite Presses
A composite press should be designed to work effectively with either a specific composite product or a range of different composites – taking into account the distinct attributes of each material involved for the best possible results.
Cambridge Dynamics provides both off the shelf and bespoke composite press solutions, most often employing advanced ball screw and servo control to provide levels of accuracy and repeatability not available from comparable hydraulic solutions.
We have spent years working with numerous different composite presses, allowing us to develop a thorough understanding of their capabilities and features. Our specialists are experts in both the use and manufacture of machines of this kind.
Environmental Factors Influencing the choice of a Servo Press over any other type of Press
Clean – Since servo-electric presses run entirely on electricity, no oil is required. Not only does this eliminate leaks and costly disposal fees, but it also ensures that cleanliness requirements are maintained for meticulous environments like labs and clean rooms and hi-tech composite manufacturers.
Easy Maintenance – Without oil tanks, pumps, valves, and hoses, servo-electric presses require fewer components to achieve force. This makes them much easier and cheaper to maintain and support than hydraulic or mechanical flywheel systems.
Energy Efficient – A large amount of electricity is required to power a hydraulic system, even when the press is idle. Servo presses use energy on-demand, yielding energy and cost savings of up to 70%.
Long Life – Using Servo driven Ball Screws ensures presses last up to 15 times longer and achieve greater load capacity than non- ball screw servo presses.
Less Noise – Motors and pumps that drive a hydraulic power unit can exceed 80 decibels. Eliminating the HPU and its components and only using power when the press is operating (on-demand), servo presses maintain a very low ambient noise level.
Why Choose Cambridge Dynamics for Your Composite Press Requirements?
Whether you require composite materials to be fabricated and shaped on your behalf or you are interested in obtaining a press of your own, Cambridge Dynamics is the place to go.
Thanks to our experience in a wide range of manufacturing fields, we are able to quickly and effectively determine the best manufacturing methods to meet your needs. In addition, we are able to provide a full manufacturing solution from tool temperature control to robotic unloading and even CNC trimming of completed parts.
The equipment we use is cutting edge – after all, we understand the importance of remaining at the technological forefront of our field in order to fabricate exceptionally high-quality products that vastly out-perform the competition.
We employ sophisticated CNC (Computer Numerical Control) machinery that can be programmed to the tightest possible tolerance in order to replicate designs precisely.
For this reason, we ask that all of our clients provide us with as much detail as possible regarding their required part or machine. This will help us to ensure the highest achievable level of precision.
To get started, all you need to do is to make contact with the team via our online contact form. We welcome any questions or requests for advice as well as manufacturing applications.
FAQ’s
What are composite presses?
A composite press is a pressing/forming machine that shapes composite materials. This process is sometimes known as ‘compression moulding’ – since it moulds the composite by compressing it. The purpose is to press two materials together without actually dissolving them into each other.
Compression or composite moulding often requires the use of a high temperature hydraulic press to bind the materials. One is referred to as the matrix, which is the ‘binder’ or ‘background’ material – it surrounds clusters of fibres/fragments of something stronger, known as the reinforcement.
The reinforcement material is so named because that’s what it does – strengthens the composite so it can withstand external forces. The matrix holds the reinforcement in place and protects it against temperature and moisture damage. The composite press is simply a tool to mould them together.
For example, fibreglass uses glass fibres as the reinforcement and plastic as the matrix. Concrete uses aggregate as a reinforcement and cement as a matrix. The way that the reinforcement particles are pressed will determine how strong the composite is in each direction (isotropic or anisotropic).
What are composite presses used for?
There are many uses for composite presses, which can manufacture composite materials for a variety of uses and industries. Compression moulding is becoming increasingly popular as a cost-effective method of producing high volumes of lightweight yet structurally strong components.
Composite press machines can reliably provide accurate composite parts with faster cycle times as an alternative to metal stamping. Most composites are fibre-reinforced polymers (FRPs) which have been matched to boost the properties of both materials (e.g. corrosion resistance and insulation).
These properties make composites useful in creating parts for structures that need to withstand extreme environments – like boat hulls, aerospace craft, and automotives. Composites such as metal oxides with excellent electrical conductivity are useful for electric cables and silicon computer chips.
Composite presses help to create durable materials for versatile purposes, from metal alloys to thermoplastics. They can form both small and large parts with basic or complex custom moulds. Composite manufacturing is a great asset when large production runs have a short lead time.
How does a composite press work?
When using composite presses, a precise metal tool must be made that will produce the desired part with the exact measurements. The high-quality matched tool, or composite mould, ensures an excellent finish. This tool is inserted into the composite press and usually heated up.
The composite materials are prepared and then inserted into the heated mould. The composite press is then activated to apply high pressure and force the composite into the required shape. It’s then left to consolidate (or cure if it’s thermosetting rather than thermoplastic, which goes in cold).
Whichever temperature is required, maintaining that constant temperature helps to speed up the process and produce more composite parts in a shorter amount of time. Further surface finishing may be required after the composite is removed from the press to clean up any excess material.
Specifically matching the metal tooling puts this service at a higher cost, which means that it’s unfortunately not a viable option for prototypes or limited runs. Composite presses also may not apply pressure from all directions like vacuum-consolidation, which may cause variable strength.